The COVID vaccines are on the brink of receiving regulatory approvals allowing their roll-out to the global population over coming months. The hypodermic needle will take center stage in the upcoming and hugely challenging logistical operation.
The following article considers the international standards, and associated quality control disciplines, that govern the manufacture of hypodermic needles.
Author: Nili Walp Marketing Manager – Vision Engineering, North America
Hypodermic is Greek for ‘under the skin’ and cannula (the needle itself) is Latin for ‘little reed’. Developed in the mid-19th century, hypodermic needles play an essential part in healthcare. Any medical device that penetrates the skin will be subjected to strictly controlled standards. Achieving a high standard of quality for medical hypodermic needles ensures fluids are accurately administered and extracted, and patients are comfortable. When it comes to hypodermic needles there are two main ISO standards, ISO 9626 and ISO 7864, which are used to ensure quality during the production process.
Due to the number of needles manufactured at a given time, automated systems are used in the inspection and testing process. In this article we examine the ISO standards and illustrate how manufacturers can meet ISO standards requiring inspection by using a range of optical and vision systems for random sample checking during the production process.
Defining ISO 9626 and ISO 7864
ISO 9626 defines the inspection and test requirements for stainless steel needle tubing, and may also apply to other medical devices where single lumen metal tubing is used. ISO 7864 defines the requirements and test methods for the needle itself. There are common conditions in these standards as well as unique requirements for each. The standards address the materials, surface finish and visual appearance, cleanliness, acidity and alkalinity limits, size designation, dimensions, stiffness, resistance to breakage and resistance to corrosion.
Materials
Before production can begin, the material itself should meet the standards outlined in ISO 15510. This ISO standard defines the acceptable chemical compositions of the material. The most common alloys are grades 304 and 316 stainless steel. The material is versatile and easy to work with, meets precise tolerances, corrosion resistant and can be subjected to rigorous sterilization methods without compromise.
Inspection tasks to meet requirements found in ISO 9626 and ISO 7864
Surface Finish, Visual Appearance and Cleanliness
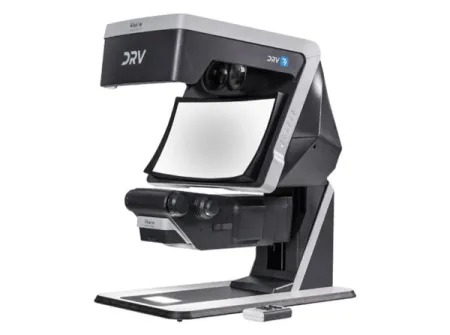
The outside surface finish of the tubing is visually inspected. The surface should be smooth and free from defects. The tube should be straight with uniform roundness. The surfaces of the tubing should be clean, without any metal and processing residue. The standards relating to these characteristics are necessary in order for the needle to function optimally without affecting the medication/specimen and causing discomfort to the patient. In order to pass the standards at this stage, an optical or digital inspection system can be used. In addition to inspection, both systems give users the option to capture images which can be used to for reporting or documentation on the batch of materials. The optical system is preferred for applications where the operator needs to perform any work on the subject since depth perception and stereo imagery is needed. An inspection system fitted with a 360-degree rotating viewer can aid in inspection as the subject can remain static while the viewer gives a 360-degree view around the area being inspected.
Size Designation and Dimensions
ISO 9626 defines the gauge size for the needle based on the nominal OD (outer diameter). Additional dimensions include the minimum and maximum OD and the wall thickness. The wall thickness will determine the flow rate and force needed for delivery or collection. ISO 7864 defines the size designation for tubular and tapered needles, the needle tube length, and wall thicknesses to determine the gauge. The benefits of using a vision system to measure the OD are improved accuracy, repeatability, reproducibility, and the ability to inspect a long portion of the needle at a time. Automatic edge detection systems help produce consistent measurements across different operators.
The length of the needle can quickly be measured using a FOV (field of view) system that is programmed with the specified length giving users a fast pass/fail result. When needles are longer than the field of view, the needle can be measured using a motorized or manual stage which will move the needle from one end to the other.
A complete set of measurements are necessary in order to define the needle’s designation. The following expression is used to identify the needle: OD (tip)/OD (hub) x Length.
Needle Point
During the manufacturing process the needle tip is ground from metal rods. The finished needle should be free from burrs on the cutting edges (outside) and the rims (inside) produced from the grinding process. If burrs exist, this may result in increased pain and prolonged healing for the patient. Needles should be inspected to determine if burrs are present after the grinding process.
Vision systems are also used to measure the bevel angle of the needle tip. The angle will determine the sharpness of the needle. Needle sharpness is significant when it comes to needle performance. A sharp needle should result in less trauma during use.
Measuring systems that use flat field telecentric optics and with controllable illumination helps create a sharp image and the ability to focus on both the bevel and the needle tip at the same time. Having a range of illumination options is critical when measuring the reflective surface of the metal. If inspection, deburring and video measurements are to be done at the same time, dual optical inspection and measurement systems are ideal for the task.
Stiffness and Resistance to Breakage
It is essential to know the strength and integrity of the needle to predict how it will react to force and discover any weak points. Flexure tests will measure how likely the needle will permanently bend or become misshapen during use. Tensile tests measure the strength of the needle as tension is applied at a determined rate. Puncture tests test the sharpness of the needle point and uniformity of the needle tube. Subjecting the needle to these tests will ensure consistent integrity of the material. Inspection is necessary to exam the needle before such tests and identify any changes to the needle after the tests.
Resistance to Corrosion
Grades 304 and 316 stainless steel is the material of choice for medical applications. The alloy is naturally corrosion resistant which means the needles can be stored in many types of conditions and are suitable for re-use since they stand up to vigorous sterilization without corrosion. Testing involves subjecting the metal to various known corrosive solutions then inspecting the material afterwards. Corrosion would be evident by any changes made to the original needle. Needles that fail corrosion resistance testing may be susceptible to corrosion caused by certain conditions, increase pain during use, enable the growth of microorganisms, and breakdown the integrity of the needle which may result in breakage during use. Optical or digital inspection at high magnification will identify any corrosion.
Needle Hub
The needle hub is the fitting at the end of the needle that connects to a syringe or other components. When inspecting the needle hub, manufacturers look at the conical fitting, (the socket of the hypodermic needle hub) and the colour of the hub. The hub colour can either be with or without pigmentation in accordance with ISO 6009. The colour of the hub will indicate the gauge of the needle as set by ISO standards. The hub should be inspected for defects and each opening measured. The hub and needle should fit tightly together. Once the correct measurement is determined, systems that can deliver a rapid pass/fail result are ideal for this application. The needle will be secured to the hub with adhesive. Using either an optical or digital inspection system will aid in examining the amount of glue added to secure the two pieces and excess glue can be removed and/or the adhesive system adjusted to suit.
Hypodermic Needle manufacturing customers of Vision Engineering use the following products in their operations:
Optical Inspection
- Lynx EVO with optional 360 degree viewer and camera
- DRV-Z1 3D digital viewer with zoom and ability to share images/video in real time to off-site locations
Digital Inspection
- EVO Cam ll – with optional 360 degree viewer
3D Stereo Digital Inspection/Display
- DRV-Z1
Measurement
- TVM – Rapid video field of view system
- Swift PRO DUO – Dual optical and video inspection and measurement system
For more information: www.visioneng.com
Tags: 3d vina, hiệu chuẩn, hiệu chuẩn thiết bị, máy đo 2d, máy đo 3d, máy đo cmm, Meeting ISO Standards in Hypodermic Needle Manufacturing, sửa máy đo 2d, sửa máy đo 3d, sửa máy đo cmm