Imagine a fully digital quality inspection process where you can inspect parts even after they have left the factory. The emergence of new technology has made this possible using a product digital twin for manufacturing quality control. Virtual sorting can eliminate physical sorting activities completely by performing quality inspection in a software environment cutting costs significantly.
What is Virtual Sorting?
Virtual Sorting refers to the digital quality inspection of manufactured parts in a software environment either for new or existing inspection points by using each part’s digital twin, without the need for the physical presence of the parts, to conduct internal and external sorting activities fully digitally.
Imagine the following scenario: You observed a decrease in process capability, which might cause quality issues with the true location of a hole. However, the hole’s location is not included in the current inspection specifications. Therefore, you now need to start a sorting activity and inspect the hole’s location for parts that have already been manufactured and, possibly, shipped.
Now, imagine that you could just open a software, define the hole’s location as a new inspection point, and immediately get inspection results in the software with the S/Ns of the non-conforming parts listed. After that, the only thing you need to do is to pass the list of S/Ns for the parts to be picked and scrapped.
And how about external sorting requests from your customers on the other side of the world? For example, a certain feature that has not been included in the inspection requirements is now causing problems at the assembly stage for your OEM customer. Without relying on third-party sorting agreements and waiting for the sorting activity to be conducted, you could immediately run the required inspections digitally on your database of product digital twins and share the list of non-conforming parts with your customer to be scrapped.
By eliminating the need for physical processes and parts, and fully digitizing the sorting process, Virtual Sorting enables new levels of operations efficiency and flexibility as well as strategic advantages that have not been possible before.
Virtual Sorting from an Operational Perspective
Conventionally, sorting activities are bound by physical parts and physical processes. Each part needs to be inspected one-by-one through some sort of physical process such as using a gauge, a checking fixture – or through visual inspection in case of presence checks for child components such as nuts and bolts.
As such, sorting activities are compulsory burdens for manufacturers in terms of costs, resources, and operational complexity. Even though established sorting processes and third-party sorting agreements exist; the required manpower, time, and the need to inspect each part one-by-one put a constraint on reducing the associated costs no matter how well these processes are streamlined.
Virtual Sorting enables manufacturers to break through such constraints imposed vy physical processes. It completely eliminates the need for accessing and moving around the physical parts to conduct inspections, and the need for dedicated man-hours to inspect parts one-by-one.
Moreover, since it is a fully virtual process, it enables quality specialists to conduct the sorting activity remotely for parts that are already shipped to global customers with facilities spread around the world – cutting not only internal but also external sorting and batch recall costs.
Considering that an OEM-requested sorting activity by conventional means can cost around USD 100k-300k depending on the part complexity and production volume, Virtual Sorting helps manufacturers significantly cut costs arising from poor quality.
Similarly, it provides almost a total payback on the investment for the quality inspection system in one sorting request – hence, providing a significantly higher return on investment over the total lifecycle of the quality inspection system in comparison to conventional systems.
Virtual Sorting from a Strategic Perspective
Virtual Sorting creates value not only in terms of operational efficiency but also strategically in the long-term. The complexity of parts, operations, and supply chains is increasing, and so are the pressures on price competitiveness, cost control, and quality performance. In response to these challenges posed by the evolving industry landscape, it becomes critical that manufacturers can have greater control over the production quality throughout the entire production lifecycle and respond to quality issues and take corrective actions immediately regardless of the facility location and production lifecycle
By removing the barriers posed by physical parts and processes, Virtual Sorting allows manufacturers to retain effective control on parts produced even after the parts leave their premises. Moreover, they can immediately respond to quality concerns and complaints that arise after the delivery of the parts – improving reputation and gaining customers’ trust while cutting costs.
Virtual Sorting Using Multi-Camera Technology
Multi-camera technology is a photography-based inspection technology that is driven by powerful machine vision and photogrammetry algorithms. It typically consists of 30 to 90 fixed, digital cameras that are located around an inspection chamber.
Unlike fixed or robotized sensor systems, the cameras do not focus on a single feature at a time but observe the whole part or large sections of the part at once. Each collected image by each camera provides views of multiple features at a time. Together, they provide a complete view of the whole part which then can be treated as a digital twin to define new inspection points and conduct new inspections. The physical part is only needed for the initial image capturing and it has no further use to conduct inspections once the images are collected – hence completely digitizing the inspection process, moving it into a 100% software environment.
All collected data is stored in a database, coupled with each part’s serial number. In case of new inspection requirements at any point of the part’s lifetime – as in the case for sorting requests – the operator simply defines the new inspection points on the CAD model of the part. Once the new inspection specifications are defined and the inspection program is set, powerful machine vision algorithms detect the inspection points on the product digital twin, which is formed from the images. Advanced photogrammetry algorithms conduct the desired measurements directly on these images for each manufactured part.
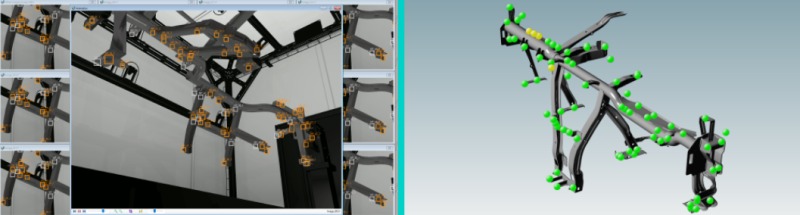
Multi-camera technology enables manufacturers to retrospectively inspect parts and conduct sorting activities in a fully virtual environment. Equipped with a patented multi-camera technology, Mapvision 100% x 100% In-Line Inspection systems provide virtual sorting capability for even the most complex and demanding parts such as underbodies, EV battery modules, and cross car beams.
For more information: www.mapvision.fi
Tags: 3d vina, Enabling Virtual Sorting With Multi-Camera Technology, hiệu chuẩn, hiệu chuẩn thiết bị, máy đo 2d, máy đo 3d, máy đo cmm, sửa máy đo 2d, sửa máy đo 3d, sửa máy đo cmm