Đảm bảo chất lượng thường là một vấn đề đau đầu đối với những người ra quyết định trong các công ty sản xuất – một tệ nạn cần thiết tạo ra chi phí cao mà không giúp cải thiện tốc độ sản xuất. Đây là một vấn đề mà Helmut Häckl, giám đốc điều hành của Schabmüller Automobiltechnik, đã quá quen thuộc. Công ty của Häckl gia công nắp đầu xi-lanh cho tất cả các loại xe động cơ xăng V6 trên toàn thế giới của một tập đoàn ô tô miền Nam nước Đức. Và họ cạnh tranh với các nhà cung cấp ở các nước có mức lương thấp. Trong những điều kiện như vậy, làm thế nào để nhà sản xuất đảm bảo mức chất lượng cao theo cách tiết kiệm chi phí? Đối với Schabmüller, câu trả lời đến từ một giải pháp đo lường tự động, với sự hợp tác chặt chẽ với ZEISS, được tích hợp trực tiếp vào dây chuyền sản xuất của họ.
Mỗi ngày, Schabmüller kiểm tra, cắt, đo lường và chuẩn bị giao khoảng 2.600 bộ phận sau khi đến nơi. “ Đây dễ dàng là dự án sản xuất lớn nhất của chúng tôi, và cũng là một dự án rất thách thức, ” Häckl nói. “Cạnh tranh toàn cầu giữa các nhà cung cấp ô tô rất khốc liệt và hiệu quả chi phí là một yếu tố quan trọng. ” Đồng thời, các thành phần phải tuân theo các yêu cầu nghiêm ngặt về chất lượng. Để giải quyết thách thức này, Schabmüller sử dụng hai máy đo sản xuất ZEISS, cùng với một bàn tải tự động, kiểm tra chất lượng của các bộ phận được sản xuất. Quá trình thiết lập của họ, hoạt động từ năm 2017, rất đặc biệt: các máy đo được tích hợp trực tiếp vào dây chuyền sản xuất tự động với sự cộng tác của ZEISS. Và khoản đầu tư nhanh chóng được đền đáp.Häckl báo cáo: “Chúng tôi chưa có một lời phàn nàn nào kể từ khi chúng tôi bắt đầu thực hiện đảm bảo chất lượng với công nghệ đo lường nội tuyến của ZEISS,” Häckl báo cáo.
Hiệu quả cần thiết trong gia công được đảm bảo bởi một dây chuyền sản xuất gần như hoàn toàn tự động: phôi đầu vào được nạp thủ công vào trạm đầu tiên và phần còn lại của quy trình gia công sau đó được thực hiện gần như hoàn toàn tự động trên tổng số 96 trạm xử lý. Quy trình chính là cắt các khoảng trống để tạo ra các lỗ khoan và bề mặt bịt kín có độ chính xác cao. Các cánh tay rô-bốt lấy các khoảng trống từ dây chuyền lắp ráp và đặt chúng vào các máy kẹp. Những gì xuất hiện cuối cùng là một bộ phận được gia công sạch sẽ. Thông thường.
Dây chuyền sản xuất tự động với hệ thống đảm bảo chất lượng tích hợp
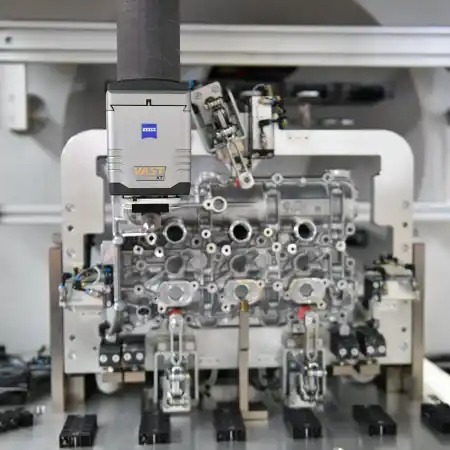
Để phát hiện các trường hợp ngoại lệ đối với quy tắc này một cách đáng tin cậy, một trạm được đặt ở giữa dây chuyền sản xuất với hai máy ZEISS GageMax tích hợp, mỗi máy được trang bị một hệ thống nạp hoàn toàn tự động. Do đó, trạm này hoạt động như một phần hoàn toàn tự động của dây chuyền sản xuất: một cánh tay rô-bốt nắm lấy nắp đầu xi-lanh đi vào và giữ nó lên để loại bỏ bất kỳ mảnh kim loại còn sót lại nào bằng khí nén. Cánh tay đặt nắp trên một thiết bị kẹp tùy chỉnh của ZEISS trên bàn trượt. Sau đó, các đầu dò trong giá đỡ đầu dò bên ZEISS ProMax-G sẽ quét các đặc điểm liên quan của thành phần theo một chương trình xác định. Bằng cách này, trạm có thể nhanh chóng quét và phân tích 35 đặc điểm cực kỳ quan trọng. Một hệ thống mã hóa cho robot tại trạm đo đó biết nên chọn một phôi để kiểm tra hay gửi nó đến trạm xử lý tiếp theo. Hệ thống này đảm bảo rằng việc kiểm tra luôn được phân bổ đều trên các phôi gia công ở tất cả 96 trạm, giúp luôn có thể theo dõi lỗi đối với các máy sản xuất và trạm xử lý cụ thể.
Tốc độ đo cao và độ bền
Nhà điều hành cơ sở Frederic Kern vô cùng hài lòng với giải pháp: “ Điều quan trọng đối với tôi là phải biết chắc chắn rằng cơ sở ‘của tôi’ đang hoạt động trơn tru và mang lại chất lượng cao. Giải pháp này mang lại cho tôi sự chắc chắn ngay lập tức.” Mỗi trong số 96 trạm xử lý trong cơ sở là một nguồn lỗi tiềm ẩn. Một lần hoán đổi công cụ có thể dẫn đến sai lệch nằm ngoài dung sai rất hẹp. “ Nếu điều này xảy ra, tôi cần biết về nó ngay lập tức, ” Kern nói, “nếu không chúng tôi sẽ sản xuất ra rất nhiều sản phẩm bị loại, và điều này rất tốn kém.”
Giải pháp đo lường tự động của ZEISS có thể kiểm tra sản phẩm của tất cả các trạm chế biến trong vòng 16 giờ. Điều này chỉ có thể thực hiện được nhờ hai máy đo sản xuất, có khả năng tải và đo các thành phần một cách nhanh chóng. Kern nói: “ Tất nhiên, có những điều kiện khắc nghiệt trong quá trình sản xuất – có bụi bẩn và rung động, trời lạnh vào mùa đông và nóng vào mùa hè. “ Nhưng các thiết bị ZEISS vẫn hoạt động tốt trong những điều kiện này.” Helmut Häckl có thể chứng thực điều này. Năm 2017, anh giám sát dự án giới thiệu máy đo tọa độ nội tuyến. “ Tôi thấy rõ ràng ngay từ đầu rằng chúng tôi cần một giải pháp nội tuyến,” Häckl nhấn mạnh. “Và giải pháp nội tuyến của ZEISS cung cấp độ bền mà chúng tôi cần trong một môi trường như thế này.”
Có thêm thời gian cho Phòng thí nghiệm Đo lường
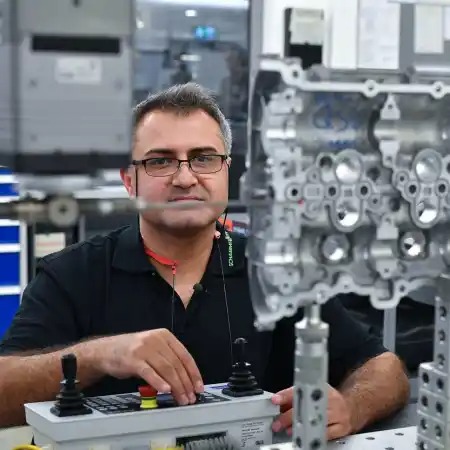
Trước khi giới thiệu giải pháp nội tuyến, việc đảm bảo chất lượng được thực hiện bằng cách thực hiện các phép đo nối tiếp trong phòng thí nghiệm đo lường – một quy trình rất tốn thời gian. Giờ đây, nhà đo lường học Emre Baysal và các đồng nghiệp của ông có đủ thời gian để thực hiện các phép đo hoàn chỉnh chuyên sâu, bao gồm độ nhám và đường viền, trên các thành phần được chọn hai lần một tuần. Baysal cho biết: “Thật tuyệt vời khi giải pháp ZEISS có thể liên tục thực hiện kiểm tra định kỳ trong sản xuất mà không cần sự tham gia của bất kỳ công nhân nào. “Điều này giúp chúng tôi tiết kiệm rất nhiều thời gian và cho phép chúng tôi tập trung vào những nhiệm vụ thực sự cần được thực hiện bởi một nhà đo lường được đào tạo.”
Baysal cũng là một fan hâm mộ lớn của phần mềm ZEISS CALYPSO mà Schabmüller sử dụng để quản lý nhiều thiết bị. Công ty cũng sử dụng ZEISS PiWeb để trực quan hóa dữ liệu chất lượng. “Đây là một lợi thế to lớn, ” Baysal nói, “bởi vì nó cho phép chúng tôi so sánh trực tiếp các kết quả đo từ tất cả các thiết bị và nó cung cấp cho chúng tôi thông tin kết luận mà chúng tôi có thể lưu trữ trong cơ sở dữ liệu của mình.”Dữ liệu được lưu trữ với ZEISS PiWeb được nén và hiển thị theo cách dễ hiểu, với dữ liệu liên quan được hiển thị trực quan cho các nhóm công nhân khác nhau (ví dụ: người vận hành máy, nhà đo lường, quản lý). Điều này đảm bảo tính minh bạch và dẫn đến việc ra quyết định nhanh chóng và dễ dàng, cho phép xác định kịp thời các xu hướng sản xuất và loại bỏ các phôi bị lỗi. Và vì công nhân của cơ sở đã quen thuộc với môi trường phần mềm nên không cần phải đào tạo thêm khi giới thiệu giải pháp nội tuyến ZEISS.
Đối với Herman Häckl, việc đảm bảo chất lượng từ chỗ là một nguồn khó chịu trở thành lợi thế cạnh tranh thực sự: “ Chúng tôi có thể đảm bảo chất lượng trong dây chuyền sản xuất lớn nhất của mình mà không phải thuê thêm nhân sự,” Häckl nói. “Điều này giúp tiết kiệm chi phí và cho phép chúng tôi sử dụng chất lượng để tạo sự khác biệt so với các đối thủ cạnh tranh từ nước ngoài.” Häckl nói: “Ngay cả việc lập kế hoạch và giới thiệu hệ thống cũng dễ dàng: “Những điều như thế này chỉ có thể thực hiện được với sự hợp tác chặt chẽ giữa các đối tác lành nghề. ZEISS hiểu nhu cầu của chúng tôi là gì, đồng thời có chuyên môn và kinh nghiệm cần thiết để tích hợp máy đo vào dây chuyền sản xuất tự động.”
Để biết thêm thông tin: www.zeiss.com/metrology
Tags: 3d vina, hiệu chuẩn, hiệu chuẩn thiết bị, máy đo 2d, máy đo 3d, máy đo cmm, sửa máy đo 2d, sửa máy đo 3d, sửa máy đo cmm