To upgrade the inspection capabilities of its measurement laboratory, the quality department at the Chassis & Safety division of automotive equipment manufacturer Continental, located in Veszpren, Hungary has invested in two LK Metrology Altera multi-sensor coordinate measuring machines (CMMs).
Continental needed a high capacity system capable of rapid inspection cycles combined with fast surface scanning and accurate feature measurements, the aim being to gain more comprehensive insight into the company’s products. The range includes electronic and hydraulic brake and chassis control systems, wheel and engine speed sensors, airbag electronics and electronic air suspension systems.
Renowned for expertise in driving safety, the firm’s quality department plays a pivotal role in its success. Day to day tasks in the measurement laboratory include feature and surface inspection, linear dimension measurements and GD&T analysis to monitor production quality from the shop floor and assist in new product development.
The quality department processes approximately 1,600 inspection reports per year, each consisting of around 20 measured parts, but they needed to gain quicker, more comprehensive insight and obtain more information per report.
Multi-Sensor Metrology Paves Way For Faster Inspection
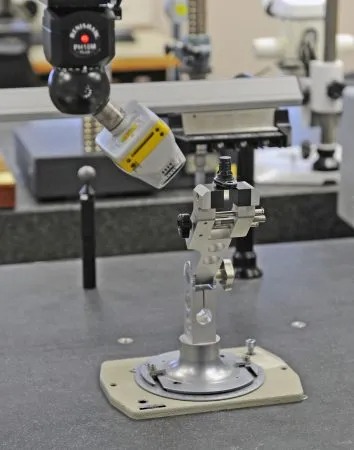
In Continental’s measurement laboratory, a single CMM with touch probes was handling most of the inspection. Measuring technician Peter Somogyi advised that the main limitation of the pre-existing CMM was its slowness and hence low capacity. Quality engineer Tamas Brunner added that the software was not up to their standards in respect of automated inspection and the latest GD&T. With so many measuring tasks to process, the CMM was unable to keep up with throughput using touch probe inspection, let alone provide the level of insight necessary. Mr. Tamas calculated that they needed to halve inspection cycle times.
Before beginning the search for a new solution, the quality department outlined its desire to utilize multi-sensor technology in the reorganization of the facilities. After consulting several CMM vendors, an ALTERA 8.7.6 CMM from LK was identified as the ideal solution. The decision was made to install two of them, each providing multi-sensor capability complemented by LK CAMIO software.
In addition to a Nikon LC15Dx digital laser scanner, the new CMMs include a Renishaw TP200 tactile measuring probe. An ACR3 change rack ensures smooth, automated exchange between tactile and non-contact probes, controlled by the CAMIO acquisition and processing software.
As all measurement data is stored and available for reprocessing or further analysis, the new inspection system serves as an important tool in handling potential customer claims. The quality of the new inspection process has introduced increased insight into critical dimensions, cavities and functional features of parts, enabling faster corrective action.
The direct benefits, such as faster inspection cycles and increased productivity as well as quick and easy report generation, are allowing Continental to meet its goals. Mr. Somogyi said, “The multi-sensor CMM allows almost all types of measurements to be completed on one machine, whereas previously we needed to use multiple inspection facilities such as tactile probe, microscope, projector and conturograph.” Tamas Brunner pinpointed the software as an important benefit. He confirmed, “The graphical reporting is quick and easy to understand. Parts need to comply to many different tolerances and the reports provide clear information.”
Since the twin, multi-sensor CMMs were installed in the quality department, the new equipment has provoked interest from Continental’s Molding Competence Center, which is evaluating how optical inspection can speed pre-production and development cycles.
For more information: www.lkmetrology.com
Tags: 3d vina, Automotive Control System Manufacturer Invests In Multi-Sensor Inspection, hiệu chuẩn, hiệu chuẩn thiết bị, máy đo 2d, máy đo 3d, máy đo cmm, sửa máy đo 2d, sửa máy đo 3d, sửa máy đo cmm