Hardware and software enhancements for Renishaw’s Equator gauging systems are set to be revealed at upcoming EMO Milano 2021 exhibition. Renishaw will showcase new hardware and software enhancements for the Equator gauging system which has been in the market for over a decade. While customers have always benefited from the speed, repeatability, and thermal insensitivity the system offers, recent changes and enhancements to the hardware and software mean some additional benefits are now available.
Many Equator system customers benefit from an integrated machine tool solution using Renishaw’s Intelligent Process Control (IPC) software, which enables inspection results to be translated into tool offset updates communicated automatically to machine controllers. This results in the ability to automatically identify and adapt to sources of process drift, such as tool wear.
Offset information collected as part of the Intelligent Process Control, as well as historical inspection data, can now be fed into the Renishaw Central manufacturing data platform. Renishaw Central provides a consistent method of connecting Renishaw measurement and manufacturing devices, including the Equator gauging system, to make it easy for a variety of systems and processes to access Renishaw device data.

By connecting multiple Equator gauging systems to Renishaw Central, manufacturers can identify sources of process variance.
John Hearfield, Product Marketing Engineer responsible for the Equator gauging system, describes the benefits of this connectivity and data pooling: “Manufacturers want to achieve consistency across their production lines by seeking out sources of process variance so that they can make informed, corrective action to achieve continuous improvement and increase efficiency. Data is key to achieving this control. Where multiple Equator gauges are integrated into manufacturing lines or cells, the connectivity with Renishaw Central provides the opportunity to identify variation in yield between the production lines, suggesting when machine maintenance may be required. It can highlight if tools are wearing faster on one machine than another, or it could highlight other sources of variance, such as those related to shift patterns or environmental changes.”
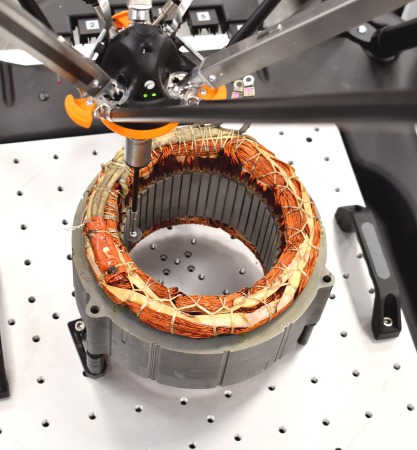
“By using Renishaw Central to couple data from Equator gauges with data from other Renishaw devices such as machine tool probes, CMM probe systems and additive manufacturing systems, Renishaw device data can be used to build a picture of the full production process, from raw material to finished product.”
To keep pace with changes to Windows software, the Equator Controller now runs on a Windows 10 platform. This means the controllers can be kept up to date with the latest Windows security updates. This feature is particularly important when networking machines as part of smart manufacturing and Industry 4.0 setups. The new Windows 10 Equator Controller also benefits from updated processors and a high specification graphics card, which delivers faster boot-up times, a more responsive feel to the graphical user interface and a sharper graphical display.
Equator 300 and Equator 500 gauging systems continue to be implemented into many automotive manufacturing processes worldwide. As the automotive industry develops electric vehicle (EV) technology and associated manufacturing processes, customers frequently face new inspection challenges. Due to its flexibility and programmability in meeting these challenges, Equator gauges are being deployed in an increasing number of automotive parts manufacturers to inspect stators and EV motor housings plus many other automotive components. This trend is certain to continue as the switch from internal combustion engines to EV gathers pace.
For more information: www.renishaw.com
Tags: 3d vina, hiệu chuẩn, hiệu chuẩn thiết bị, máy đo 2d, máy đo 3d, máy đo cmm, Renishaw Equator Gauging Systems Receive Hardware and Software Enhancements, sửa máy đo 2d, sửa máy đo 3d, sửa máy đo cmm