“The aerospace metrologist knew what he was up against: a one-thousandths of an inch clearance on the deployment of the solar power array. An undeployed solar array would mean, of course, mission failure”. The question came down to whether this metrologist could trust the accuracy of his laser tracker – in his location and at that moment.
Relying on the relative positions of components within the instruments, laser trackers and laser radars are highly accurate and extremely sensitive mechanical systems. Environmental hardships, wear-and-tear from frequent usage, shipping an instrument, even multiple end-users, and simply the age of the instrument can create internal misalignments that degrade measurement accuracy and challenge the integrity of past and future measurements.
Interim field testing for laser trackers and laser radars was needed long before 2014 when NIST first developed the IR-8016 test providing a volumetric check of these precision instruments.
Brunson Instrument Co., working alongside NIST, created the KinAiry System – a 2.3-meter carbon composite reference bar and software -and the roughly 30-minute NIST IR-8016 process has been providing peace of mind for metrologists since KinAiry was introduced the year later. The KinAiry Report, a graph portraying a tracker’s performance versus the manufacturer’s specifications, has since become a staple in metrology applications across the globe.
More recently, the ISO-10360 release (31 August 2020) added a field-testing process to the ISO standard with a slight variation from the NIST process. (See the “ISO guidelines for Frequency of Interim Field-Testing,” below.)
Below are three application stories featuring metrologists utilizing the KinAiry System.
Before the Launch
A few years ago, KinAiry was involved in a real-life drama surrounding the assembly of a critical satellite. With the launch window approaching, the aerospace metrologist knew what he was up against: a one-thousandths of an inch clearance on the deployment of the solar power array.
The solar array would nest in the satellite’s fuselage for launch, of course, but, once in orbit, would need to clear that tight tolerance as it deployed into position. A satellite with no power was not an option: This measurement challenge was the very definition of a mission-critical measurement.
With this extreme-tolerance measurement looming, the metrologist knew, for his peace of mind, that he would need to completely trust his laser tracker to measure the clearance accurately.
The laser tracker that would conduct the measurement had been shipped to the launch site, so there was a risk that normal in-transit vibrations had thrown off critical components. But a KinAiry reference bar was also shipped along with the tracker.
Brunson’s KinAiry system provided a volumetric check of the tracker, right on the satellite assembly floor, to ensure that the instrument was operating within the manufacturer’s specifications. The 30-minute test was run just before the critical measurement, and just after. The tracker was in good shape, the launch proceeded, and the solar array deployed and has operated smoothly for two years now. Mission accomplished.
“All’s well that ends well,” said the metrologist. “But I can tell you, just the thought of an in-orbit failure due to an errant measurement instrument made me lose sleep before we adopted the KinAiry system.”
“You can’t underestimate the value of maintaining confidence in your tracker,” he observed.
The Metrology Service Provider – Shipping A Sensitive Instrument
3 Space, Inc is a busy metrology service provider operating out of a storefront on Florida’s Space Coast. Although their work frequently finds them in nearby space production and assembly facilities, they also travel far and wide to serve metrology customers in the automotive, power generation and shipbuilding industries.
The travel and occasionally rugged operating conditions can take a toll on the company’s fleet of laser trackers. “When shipping cases arrive back at our shop all chewed up, it raises concerns for the tracker’s performance,” said company president Mike Gunn, “We have to be confident in our instruments.”
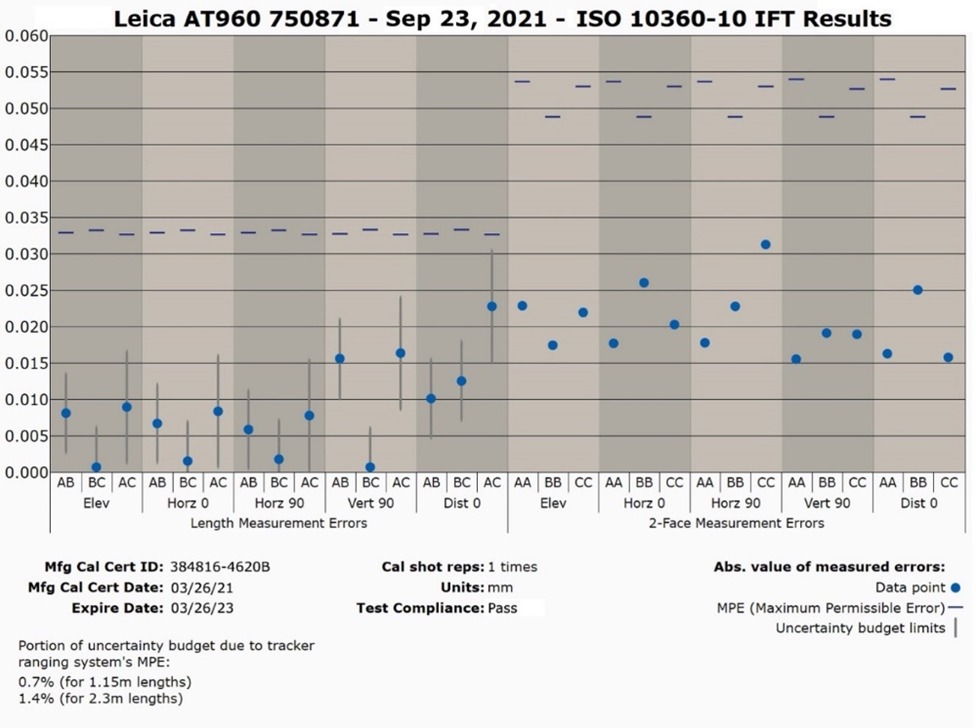
In the past, when the company’s metrology engineers had concerns about a tracker’s performance, the only option was to send the unit in for factory calibration, removing the suspect tracker from service for a week to 10 days. “And we’d still worry that the instrument was thrown off when it was shipped back,” the company’s lead field engineer noted.
“Now, with the KinAiry system, we keep a clear performance record for each tracker,” Gunn commented. The company’s quality system now calls for running a 30-minute KinAiry test on each tracker before it goes out on each service job, and they adhere to a monthly schedule for testing.
“We are working on complex, dynamic and unique challenges at each customer location,” Gunn concluded, “When we can maintain confidence in our trackers, it’s one less worry.”
Important Tool In The Quality Process
The aerospace tooling manufacturer runs a rigorous Quality Program, running daily compensation routines on their fleet of 11 trackers. The company’s laser tracker manager has added KinAiry to the routine, conducting an interim field test quarterly on each tracker and as needed when measurement issues arise.
“We also follow a strict annual calibration cycle and run a KinAiry test on each tracker when it arrives back from the manufacturer’s calibration cycle,” he said. One tracker, upon returning, failed the KinAiry test, likely due to rough handling by the shipper.
The tracker manufacturer was able to diagnose the problem from the KinAiry Report (see image) and the tracker was repaired, and upon return, passed the KinAiry test.
“When the KinAiry Report was accepted by the manufacturer, this was further validation of our quality process,” he noted. “As a company, that peace of mind is important to us, and the KinAiry system has become an important tool in our quality process.”
For more information: www.brunson.us
Tags: 3d vina, Field Testing System Delivers Laser Tracker ‘Peace of Mind’, hiệu chuẩn, hiệu chuẩn thiết bị, máy đo 2d, máy đo 3d, máy đo cmm, sửa máy đo 2d, sửa máy đo 3d, sửa máy đo cmm