Thousands of components and products made for automotive, aerospace, medical, and consumer electronics have specific demands on surface quality, both for cosmetic and functional purposes. From a cosmetic perspective, how something appears or feels to a customer affects its value and its overall quality impacting the way a consumer perceives a brand, its reputation and quality. Many components also rely functionally on the quality of the surface. Defects can affect both performance and reliability such as a scratch on a jet engine airfoil could cause cracking on the surface and eventual engine failure.
Conventional Visual Inspection
Still completed manually in most industries, the result of conventional human visual inspection for manufactured parts is highly variable. It is more than just observation and making a quick decision. It requires time, material knowledge and experience, proper vigilance, and an understanding of what characteristics to look for. This quality checking process is inconsistent, not easy to maintain, and not Industry 4.0 compliant, which requires high levels of accuracy and closed loop traceability.
Automated Options
Today, some automation technologies capture and determine surface quality using visual scanning techniques; however, performance is often unreliable when it comes to varying finishes, colors, and complex part shapes. Complex geometries, especially in combination with any surface finish, including highly reflective surfaces, are now possible to inspect with the ZEISS SurfMax. The solution-based system utilizes custom ZEISS optical technology, machine learning and automation. This combination provides reliable, consistent visual defect inspection that integrates into existing workflows, enabling process feedback and preventing defective parts from reaching customers.
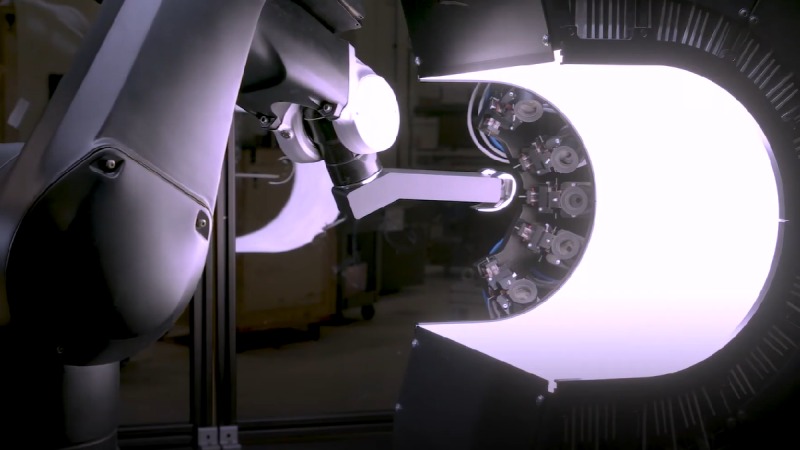
Machine Learning
Machine learning utilizes computer algorithms and statistical models to perform a specific task without using explicit instructions, relying on patterns and inference instead. As a subset of artificial intelligence, this science is used by ZEISS SurfMax within its neural network to reliably and accurately classify defects in real time.
The ZEISS SurfMax is a ground-breaking quality assurance solution for reliable high-speed visual defect detection. Integrating a perfect combination of deflectometry-based, high-resolution ZEISS optical sensors and machine learning, driven by in-house developed algorithms, the ZEISS SurfMax can detect and classify relevant surface defects in products – consistently and in real time.
Objective and Repeatable Results
ZEISS has accumulated a vast library of application experience in visual inspection, building the machine algorithms to detect and classify all relevant surface defects. Variable sensitivity can be set to customer requirements to determine the defect and severity threshold. ZEISS SurfMax is repeatable and reliable, preventing overkill, improving yield as compared to traditional inspection methods. It uses scripted parameters to classify the severity of defects and yields consistent results. What may have been a subjective assessment is now objective and repeatable with the ZEISS SurfMax preventing ‘escapes’ where bad parts are accepted by current methods.
ZEISS SurfMax catches defective parts based on defined acceptance criteria. Mistakes are avoided and parts that do not pass inspection can be removed. Corrective actions can be identified and implemented on the manufacturing process, improving yield and reducing costs.
ZEISS SurfMax takes images with different modalities, namely Grayscale, Gloss and Slope, to ensure complete capture of relevant surface characteristics. ZEISS SurfMax produces three unique and robust image channels that are essential in extracting the minute differences between real defects and acceptable surface anomalies, such as surface contamination or actual defects. Only by combining all three channels of information is it possible to detect and separate defect classes and align to the visual inspection process. ZEISS SurfMax evaluations can distinguish the smallest differences between similar defects, highlighting and classifying even the most minute changes on a part surface.
Inline Inspection For High-Throughput Manufacturing
The ZEISS SurfMax S series solves the need for quick and accurate visual inspection of prismatic parts possessing a relatively uniform cross section, such as industrial components and consumer electronics assemblies. ZEISS SurfMax uses a fixed stage with a very consistent linear path, allowing for fast and repeatable scanning. Operation is simple and automated; parts can be identified with a barcode system and results viewed in ZEISS PiWeb or exported to alternative reporting systems of choice.

Two models are available depending on the size of the parts for inspection: ZEISS SurfMax S150 for parts with a width up to 150mm and ZEISS SurfMax S250 for parts with a width up to 300mm. Isolated point-like defects with a lateral size of 25 µm can be consistently detected
by ZEISS SurfMax S Series.
Inline Inspection of Complex Geometries
ZEISS SurfMax R Series is designed to provide inspection of more complex part geometries or multiple variants of a part within a given part family. Automatic robot handling allows for consistent and optimized part alignment within the inspection tunnel for accurate and repeatable inspections.
For more information: www.zeiss.com/metrology
Tags: 3d vina, Deep Learning Delivers Automated Surface Defect Detection, hiệu chuẩn, hiệu chuẩn thiết bị, máy đo 2d, máy đo 3d, máy đo cmm, sửa máy đo 2d, sửa máy đo 3d, sửa máy đo cmm