5가지 품질 관리 도구 – 3D Vina
5가지 품질 관리 도구는 성공적인 생산을 달성하기 위해 제품 수명 주기 전반에 걸쳐 품질 시스템의 구성 요소로서 매우 중요한 역할을 합니다. 그렇다면 그 5가지 도구는 무엇일까요? 그 역할은 무엇입니까? 아래 기사에 정답이 있을 것입니다.
품질 관리의 5가지 도구는 무엇입니까?
경쟁이 치열한 자동차/제조 환경에서 조직은 동시에 3가지 중요한 목표에 직면해 있습니다.
고객의 기대를 충족하거나 초과하는 고품질 제품 제공
지속 가능한 대량 생산
정시에 배달
이 세 가지 목표를 모두 잘 달성하기 위해 QMS(품질 관리 시스템) IATF 16949 표준이 개발되어 이러한 산업에 지침을 제공합니다. IATF 16949의 특정 기대는 품질 관리의 5가지 도구에 의해 지원됩니다. 이 5가지 도구를 올바르게 적용하면 조직이 세 가지 목표를 모두 달성할 수 있는 부가 가치 방법 및 기술이 됩니다.
그렇다면 품질 관리의 5가지 도구는 무엇입니까?
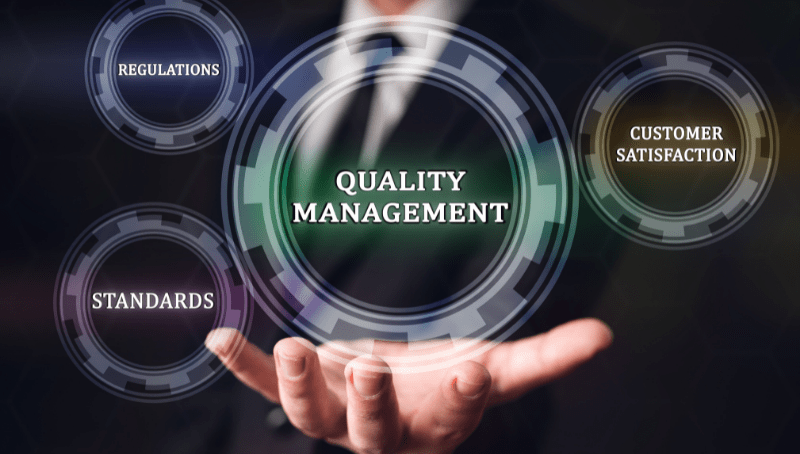
품질 관리의 5가지 도구는 IATF 16949의 기대치를 지원하는 5가지 보완 기술 및/또는 방법으로 이해됩니다. 이러한 도구는 AIAG(Automotive Industry Action Group)를 통해 제공되는 5가지 매뉴얼의 출판을 통해 별도로 문서화되었습니다. 제품 또는 프로세스를 설계할 때 사용하는 순서대로 나열된 5가지 품질 관리 도구(5가지 핵심 품질 도구):
APQP: 고급 제품 품질 계획
FMEA: 효과 분석 및 오류 모드
MSA: 측정 시스템 분석
SPC: 통계적 프로세스 제어
PPAP: 제품 부품 승인 프로세스
품질의 5가지 핵심 도구에 대해 알아보십시오.
고급 제품 품질 계획(APQP)
고급 제품 품질 계획(APQP)은 고객 요구사항을 성공적으로 충족하는 신제품 및 프로세스를 수립합니다. APQP는 고객의 관점에서 중요한 품질 하위 시스템을 식별하는 데 도움이 됩니다. PPAP는 APQP 프로세스 및 기술의 결과물입니다.
APQP의 5단계는 다음과 같습니다.
프로그램의 계획 및 정의 단계
제품 설계 및 개발 검증 단계
공정 설계 및 개발 검증 단계
제품 단계, 프로세스 및 생산 피드백
시작, 평가 및 시정 조치 단계.
FMEA(고장 모드 및 영향 분석)
FMEA(Fault Mode and Impact Analysis)는 시스템 오류의 잠재적 위험을 평가하고 식별 가능한 오류 영향에 대한 위험 감지, 예방 및 완화 계획을 권장합니다. 이 방법은 더 우수하고 안정적인 품질 관리를 위한 귀중한 통찰력을 제공합니다. 다양한 유형의 FMEA가 생산 공정의 다양한 단계 또는 투입물에서 위험을 평가하기 위해 존재합니다.
DFMEA(설계 실패 모드 및 영향 분석):
DFMEA는 제품의 최종 사용자와 제품을 유통하는 비즈니스에 중대한 영향을 미치기 전에 부품의 잠재적인 설계 결함을 감지하는 데 사용됩니다. 전체의 한 부분에 있는 설계 결함은 광범위한 제품 리콜로 이어지는 도미노 효과를 일으킬 수 있습니다.
공정 실패 모드 영향 분석(PFMEA):
PFMEA는 제조업체에서 물리적 부품 제조로 인한 잠재적인 오류를 감지하는 데 사용됩니다. 프로세스의 모든 단계는 잘못될 수 있는 모든 것을 식별하기 위해 신중하게 분석됩니다.
측정 시스템 분석(MSA)
측정 통계 분석(MSA)은 측정 시스템이 정확한 측정을 수행할 수 있는지 확인하기 위해 R-R 미터와 같은 통계 도구를 사용하는 방법입니다. MSA의 목적은 선택한 측정 시스템이 반복성과 재현성을 통해 신뢰할 수 있는 결과를 제공하도록 하는 것입니다.
통계적 프로세스 제어(SPC)
통계적 프로세스 관리(SPC)는 실행 가능한 품질 지향 데이터의 형태로 제조 프로세스 또는 제품의 측정치를 수집하는 방법입니다. 이 데이터는 공정 제어 및 생산 품질 수준을 모니터링하는 데 사용됩니다. SPC는 조직이 제조 프로세스의 품질 출력을 제어하기 위한 예방 전략을 구현할 수 있도록 하는 일종의 피드백 시스템입니다.
SPC 시스템의 네 가지 요소는 다음과 같습니다.
프로세스
성능 정보
진행 중인 조치
출력에 대해 조치를 취하십시오.
제조 부품 승인 프로세스(PPAP)
PPAP(Manufacturing Parts Approval Process)는 자동차 및 항공우주 산업의 표준화된 프로세스로 제조업체와 공급업체가 생산 전, 생산 중, 생산 후 설계 및 프로세스를 전달하고 승인하는 데 도움이 됩니다. PPAP 제품 제조 프로세스 승인 요구 사항은 일반적으로 다음 5단계로 구분됩니다.
수준 1: PSW(부품 보증) 클레임만 고객에게 전송됩니다.
수준 2: 부분 샘플 및 제한된 지원 데이터가 있는 PSW
레벨 3: 전체 지원 데이터 및 부품 샘플이 포함된 PSW
레벨 4: 고객이 제안한 PSW 및 기타 요구 사항
레벨 5: 공급업체의 생산 현장에서 검토할 수 있는 전체 지원 데이터 및 부품 샘플이 포함된 PSW.
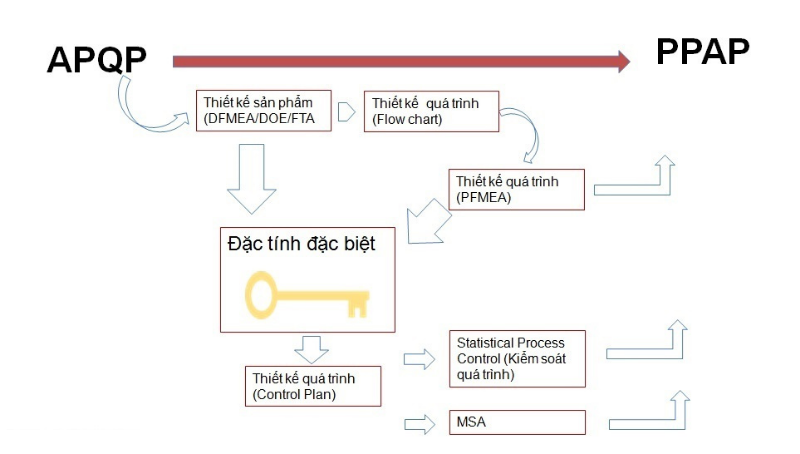
5가지 품질 핵심 도구의 적용 순서
5가지 품질 핵심 도구의 적용 순서는 아래 다이어그램에 나와 있습니다.
따라서 첫 번째로 사용되는 도구는 APQP이고, 그 다음이 제품 설계, 프로세스 설계(FMEA), SPC, MSA, 마지막으로 PPAP 프로파일입니다.
IATF 16949의 경우 위 다이어그램에 따라 각 단계에 5개의 핵심 도구가 적용됩니다. 또한 품질 관리 시스템이 항상 통제되고 개선된다는 사실을 항상 기억해야 합니다. 그래서 양산(Mass Production)에 들어갈 때 항상 이러한 도구들이 적용된다.
위는 3D Vina에 대한 품질 관리 도구 5개에 대한 공유입니다. 관리를 지원하고 비즈니스의 품질 관리 시스템을 개선하는 데 도움이 되는 유용한 지식을 많이 얻을 수 있기를 바랍니다. 질문이 있으시면 언제든지 저희에게 연락해 주십시오.
Tags: 2d he 682 미터, 2d 게이지 수리, 2d 기본 200 미터, 2d 기본 300 미터, 2d 기본 400 미터, 2d 기본 500 미터, 2d 미터, 2d 울트라 30 게이지, 2d 울트라 400 게이지, 2d 울트라 500 게이지, 2d 울트라 600 게이지, 2d 울트라 미터, 2d 피크 300 미터, 2d 피크 400 미터, 2d 피크 미터 500, 3d 게이지 수리, 3d 미터, 5가지 품질 관리 도구 – 3D Vina, cmm 게이지 수리, cmm 미터, CNC 부품 측정, 비트 게이지, 퀵 게이지 Avant 100, 플라스틱 부품 측정