ISRA VISION has introduced PouchSTAR, a new inspection system for pouch battery cells. This system is a new addition to the company’s product family for use in the production of lithium-ion batteries. With this expansion, ISRA VISION now allows manufacturers to monitor every aspect of the entire battery production process, helps them to identify problems and defects at an early stage, enabling them to meet even the most stringent of quality requirements. High-performance battery cells come in three different designs namely pouch cells, cylindrical cells, and prismatic cells, all of which are densely packed in battery assemblies for electric vehicles.
Lithium-ion batteries for electric vehicles have to meet particularly high requirements when it comes to safety and performance. It is, therefore, crucial to monitor the entire battery cell production process in order to ensure these vehicles have a reliable power supply and can run safely. For this reason, ISRA VISION has developed an innovative turnkey solution for the inline and offline inspection of pouch battery cells, which allows processes and product quality to be comprehensively monitored.
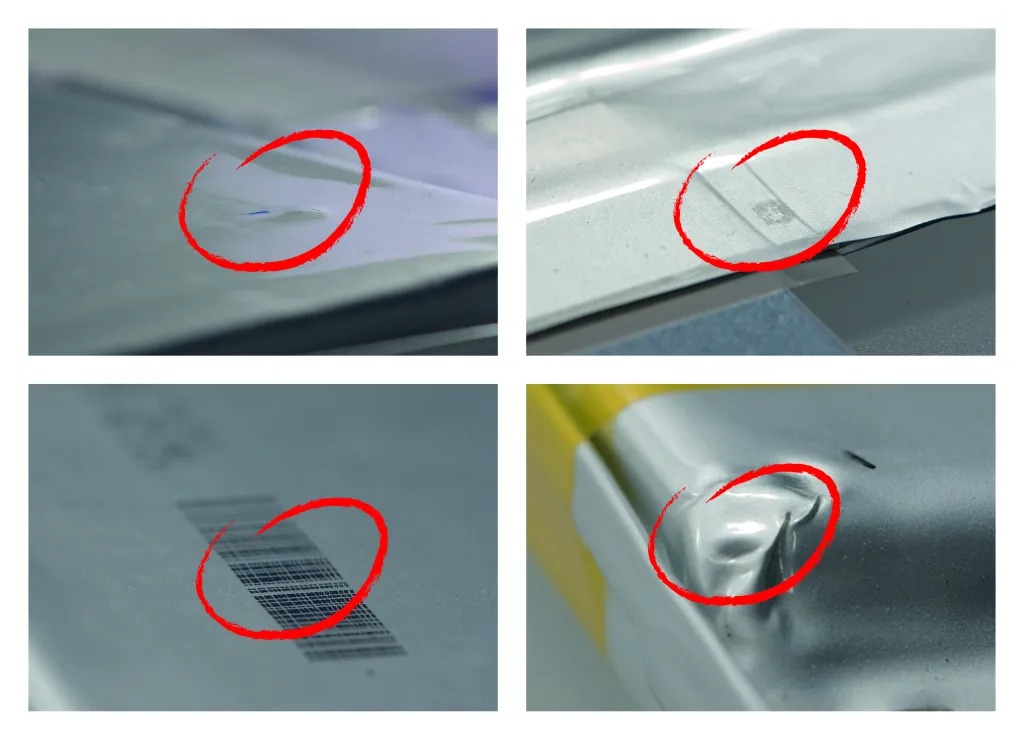
PouchSTAR comprises the very latest LED lighting technology and a high-resolution matrix camera developed by ISRA VISION. The high-performance hardware complements an extensive software package for classifying and analyzing the visually captured data. Automatic camera calibration and the built-in GigE Vision high-speed interface make PouchSTAR incredibly easy to set up and integrate into a completely networked smart factory at full production speed.
Directly integrated into the production line, the system facilitates the 360° inspection of pouch cells. It is typically used during the cell assembly process and after degassing to detect 2D and 3D surface defects such as dents, bumps, scratches, wrinkles, and contamination caused by electrolytes, for example. The system reliably detects defects on corners and edges too. PouchSTAR also inspects the shape, size, and sealed seams of the cells.
Another feature of the new PouchSTAR inspection system is its ability to automatically check and document bar codes and data codes using a built-in OCR engine. This ensures that only perfect cells are supplied to customers, helping to prevent costly recalls. Thanks to this track-and-trace feature, should a problem occur, then product qualities can be traced back in order to optimize the manufacturing process.
Entire Battery Production Process Inspection Solutions
ISRA VISION offers manufacturers of lithium-ion batteries other inspection solutions in addition to its new PouchSTAR. One example is a variation of the well-known SMASH series that is specially tailored for automatic inspection of electrode coatings, as well as separator foils and their coatings (e.g., PVDF). Over 1000 units of this advanced all-in-one solution have already been installed worldwide.
The solution delivers real-time information on product quality and shows to what extent the relevant specifications have been met. As such, it allows potential material and product defects that could compromise the quality of the end product to be detected and classified as early as the preliminary stage of battery production. In particular, its reliable inline classification, for example the differentiation between ‘black spots’ and holes that appear dark, ensures maximum safety and confidence in our customers’ products. As a result, costly and time-consuming lab tests are mostly outdated.
For more information: www.isravision.com
Tags: 360° Inspection Solution For Battery Cell Production Launched, 3d vina, hiệu chuẩn, hiệu chuẩn thiết bị, máy đo 2d, máy đo 3d, máy đo cmm, sửa máy đo 2d, sửa máy đo 3d, sửa máy đo cmm